Phosphate granulation equipment processes powdered or liquid phosphate raw materials into granular products with certain shapes and particle sizes through various technical means to meet different industrial application needs. The working principles of different types of granulation equipment have their own characteristics. Below are some common ones introduced in detail.
Working principle of disc granulator
The disc granulator is mainly composed of a driving device, a granulation disc, a scraper device, and other parts. During operation, the motor drives the granulation disc to rotate around a horizontal axis at a certain speed through a transmission device. Powdered phosphate raw materials and binders (if any) are added from the upper part of the granulation disc in a certain proportion.
Under the combined action of centrifugal force, frictional force, and gravity, the material forms a constantly rolling motion state inside the granulation disc. In the initial stage, small powdery materials come into contact with each other and gradually form small particle nuclei through surface adsorption and agglomeration under the action of a binder. As the granulation disk continues to rotate, these particle cores constantly come into contact and collide with newly added materials, and the materials will continuously adhere to the surface of the particle cores, causing the particles to gradually grow.
The scraper device installed inside the granulation disc will scrape off the materials attached to the disc wall and bottom, ensuring that the materials can roll and granulate evenly inside the disc, avoiding material accumulation. When the particles reach the appropriate size, due to the inclination angle of the granulation disc, qualified particles will overflow from the edge of the disc, completing the granulation process.
Working principle of rotary drum granulator
The rotary drum granulator consists of a rotary drum, a transmission system, a feeding device, a discharging device, a plate copying device, and other components. Powdered phosphate raw materials and additives (such as binders, lubricants, etc.) are metered and transported to the drum through the feeding device. The drum rotates around its own axis at a certain speed under the drive of the transmission system.
During the rotation of the drum, the internal plate will continuously pick up and throw down the material, causing it to form a motion trajectory similar to throwing and rolling inside the drum. During the movement of materials, collisions, friction, and compression occur between them. Powdered materials gradually aggregate into particles through the action of binders. As the drum continues to rotate, the particles roll and interact with each other, further compacting and forming, and the particle size gradually increases.
The temperature and humidity conditions inside the drum can also affect the granulation process. By controlling the hot air or steam introduced into the drum, the dryness and viscosity of the material can be adjusted to promote the smooth progress of the granulation process. Finally, qualified particles are discharged from the discharge end of the drum.
Working principle of spray granulator
Spray granulator is mainly composed of feeding system, atomizer, drying tower, collection system, etc. Liquid phosphate raw materials (such as phosphate solutions or pre treated liquid mixtures) are transported to the atomizer through a feeding system under pressure or centrifugal force.
The atomizer is a key component of spray granulation. According to different atomization methods (such as pressure atomization, centrifugal atomization, and air flow atomization), liquid raw materials are dispersed into numerous small droplets, which greatly increases the surface area of the liquid. After entering the drying tower, these droplets come into full contact with hot air, which transfers heat to the droplets, causing the moisture in the droplets to quickly evaporate and achieve the drying process.
During the drying process, solutes in the droplets gradually concentrate and precipitate, forming solid particles. Due to the small particle size of fog droplets, the drying speed is extremely fast, and the transition from liquid to solid particles can be completed in a short period of time. The dried particles are discharged from the bottom of the drying tower under the action of gravity and collected by the collection system. The hot air carrying moisture is discharged from the top of the drying tower and can be recycled or discharged after purification treatment.
Working principle of other granulation equipment
In addition to the common granulation equipment mentioned above, there are also some special granulation methods. For example, an extrusion granulator uses the squeezing effect of a screw or piston to force mixed phosphate materials through a mold head with a certain shape and size, forming strip shaped materials, which are then cut into particles of a certain length by a cutting blade; The melt granulator heats the phosphate raw material to a molten state, and then sprays it into the granulation tower through a nozzle. Under the action of air cooling, the molten material quickly solidifies into particles.
Different types of phosphate granulation equipment, based on their unique working principles, can meet the needs of different production scales, product quality requirements, and process conditions, and play an important role in the field of phosphate processing.
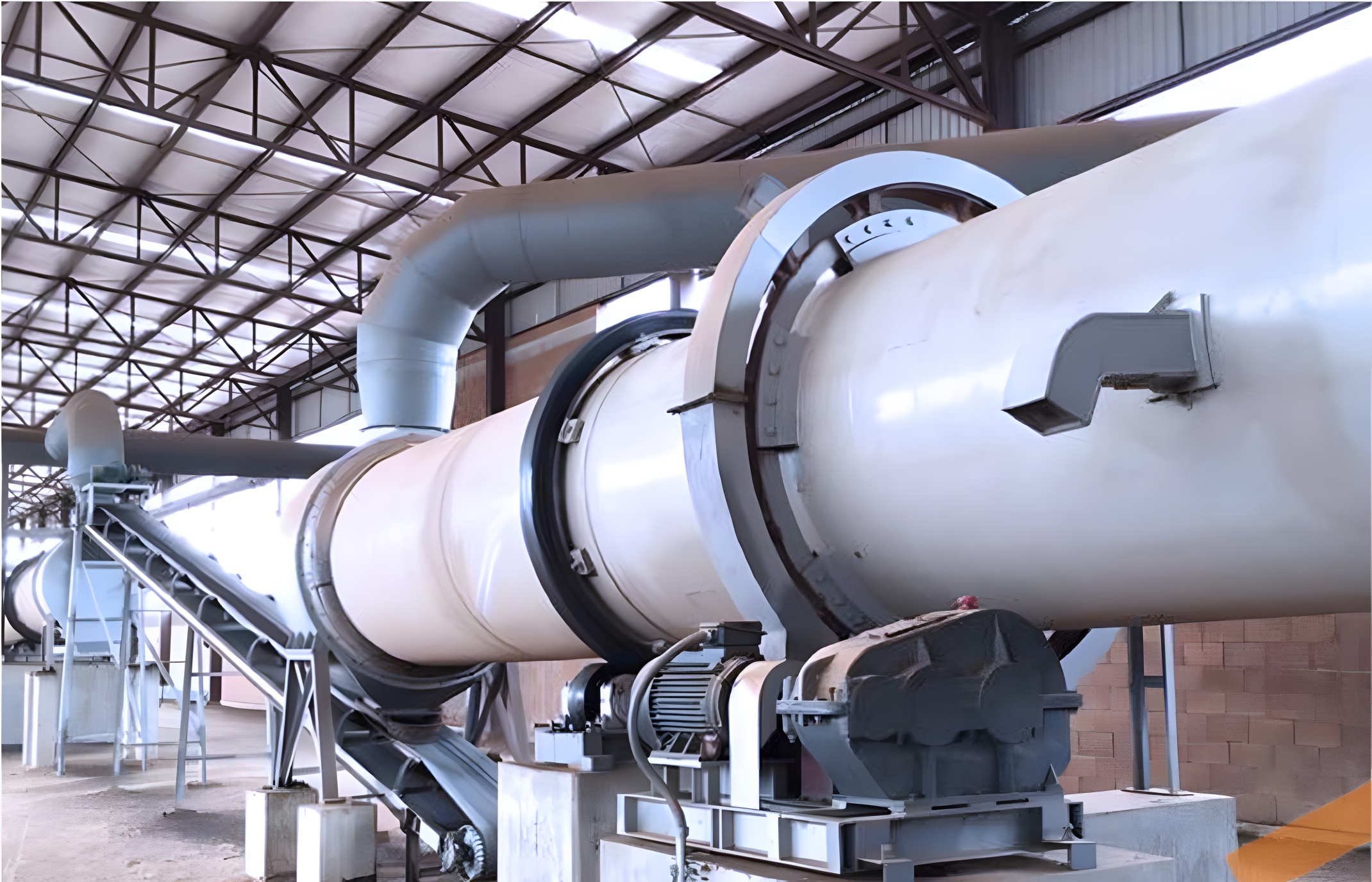