How is blended fertilizer produced?The production process of bulk blending fertilizer (also known as BB fertilizer) is to physically mix multiple elemental fertilizers or compound fertilizers according to a specific formula without undergoing chemical reactions, ultimately forming a uniform mixed granular fertilizer. The production process emphasizes the precision of raw material ratio and the uniformity of mixing, with the following specific steps:
1、 Preparation before production
Raw material selection and inspection
According to the target formula (such as nitrogen phosphorus potassium ratio, whether to add trace elements, etc.), select suitable elemental fertilizers or basic fertilizers. Common raw materials include:
Nitrogen fertilizers: urea, ammonium chloride, ammonium sulfate, etc;
Phosphate fertilizers: superphosphate, superphosphate, monoammonium phosphate, etc;
Potassium fertilizers: potassium chloride, potassium sulfate, etc;
Medium and trace elements: corresponding salts or oxides of calcium, magnesium, sulfur, iron, boron, etc.
The raw materials need to be screened, crushed (if the particles are too large), and dried (the moisture content is usually controlled below 2% to avoid clumping) to ensure uniform particle size (usually 2-4mm), and purity, moisture and other indicators should be tested to avoid impurities affecting product quality.
Formula design
Determine the proportion of each raw material based on crop demand, soil fertility data, or agricultural standards. For example, the formula for mixed fertilizer for wheat may be "20-10-10" (nitrogen 20%, phosphorus 10%, potassium 10%), and the addition amount of each raw material is calculated and input into the control system as the core parameters of production.
2、 Core production process
Step 1: Raw material storage and transportation
Storage: The processed raw materials are stored in different storage bins (such as urea bin, potassium fertilizer bin, etc.), which need to have anti caking and anti bridging functions (such as installing vibration devices or tilting bottom plates) to ensure stable feeding of the raw materials.
Transportation: Raw materials are transported from the storage bin to the batching system through equipment such as screw conveyors and belt conveyors. During the transportation process, it is necessary to avoid moisture or contamination of the raw materials.
Step 2: Precise ingredients
According to the formula requirements, quantitative weighing of each raw material through an electronic weighing system is a key step in ensuring the quality of blended fertilizers
The raw materials are fed into the weighing hopper by feeding devices (such as spiral feeders and vibrating feeders), and electronic sensors monitor the weight in real time. Once the set value is reached, the feeding will automatically stop;
The accuracy of ingredients usually requires an error of ≤± 1%. For small doses of raw materials such as trace elements, high-precision micro feeding equipment (such as micro screw feeders) should be used to ensure accurate proportioning.
Step 3: Mixing and Stirring
Send various prepared raw materials into the mixing equipment, and mix different particles evenly through mechanical action. The core requirements are high mixing uniformity (coefficient of variation CV ≤ 5%) and low particle crushing rate (≤ 3%):
The commonly used equipment is a drum mixer or a double axis gravity free mixer:
Drum mixer: The drum rotates to drive the raw materials to roll up and down, and move axially. The mixing process is gentle and suitable for raw materials with easily broken particles;
Double axis gravity free mixer: Strong convection is generated by the blades rotating in the opposite direction of the double axis, resulting in fast mixing speed (usually 3-5 minutes/batch) and higher uniformity, making it suitable for large-scale production.
The mixing time is adjusted according to the characteristics of the raw materials and the type of equipment, usually 2-10 minutes, to ensure no local aggregation of raw materials.
Step 4: Finished product transportation and temporary storage
The mixed fertilizer is transported to the finished product storage bin through lifting equipment such as bucket elevators and screw elevators. During the temporary storage process, attention should be paid to ventilation and moisture prevention to avoid clumping.
Step 5: Quantitative packaging and storage
The packaging system uses an automatic quantitative packaging machine to pack finished products into packaging bags according to the set weight (such as 25kg, 50kg), while completing the sealing process (using a sewing machine or heat sealing machine);
After the packaged products undergo quality inspection (such as sampling for nutrient content and uniformity), they are stored in the finished product warehouse, which should be dry, ventilated, and avoid direct sunlight and rain.
LITO Technology has rich research and development experience in the mixing and packaging of powder, liquid, and granular materials, as well as rich equipment production experience. The equipment is exported to various countries around the world and can provide you with perfect solutions.
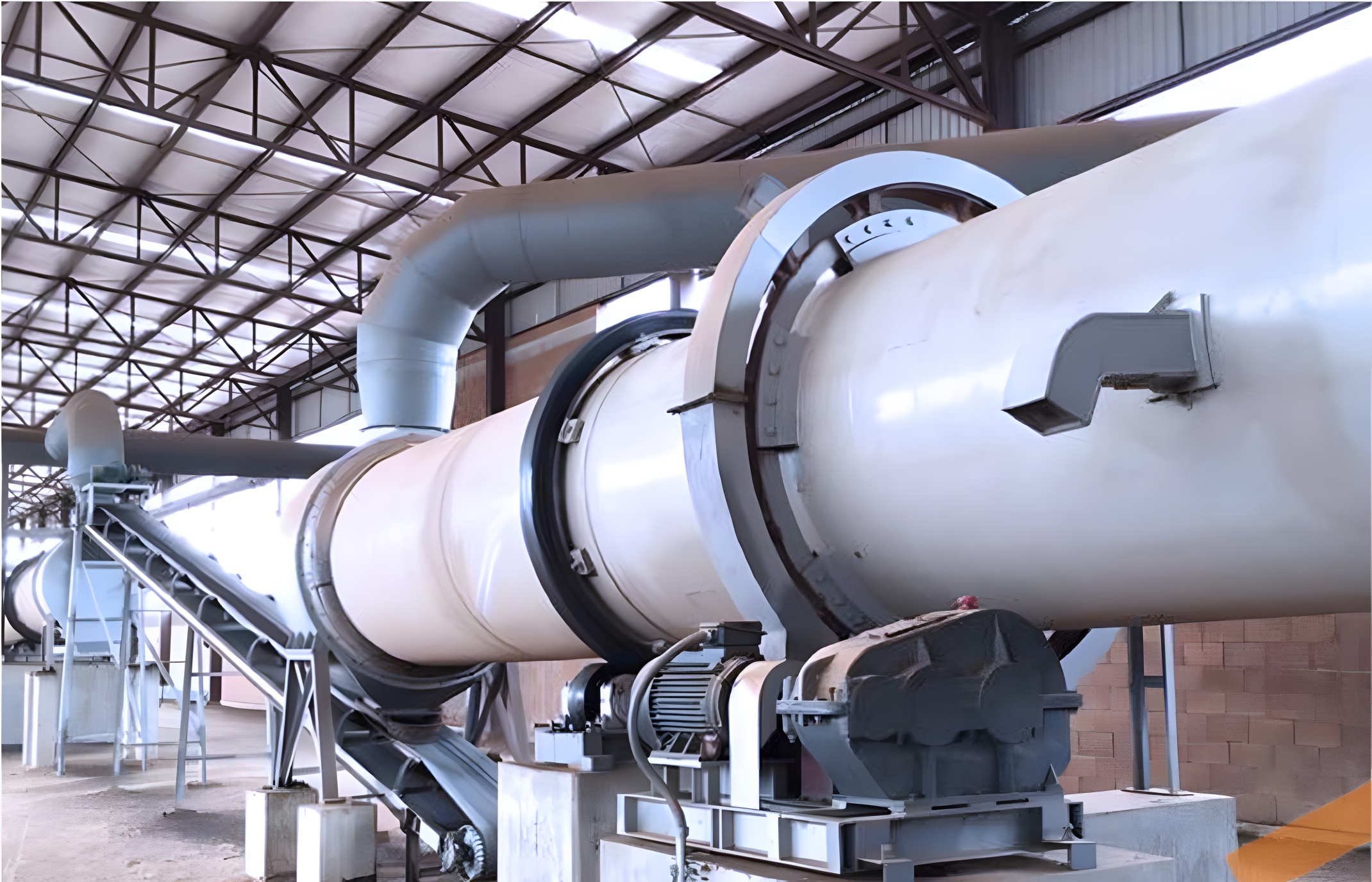
